1.0 PURPOSE:
2.0 SCOPE:
This procedure is applicable for handling of excess materials return from user department in Warehouse of (company name).
3.0 DEFINITIONS:
Nil.
4.0 RESPONSIBILITY:
4.1 Warehouse personnel are responsible for handling of excess material return from user department.
4.2 User Department personnel are responsible for returning of excess material after completion of batch on material return note.
4.3 QA personnel are responsible for approval material return note.
4.4 Warehouse Manager / Designee are responsible for compliance of this SOP.
5.0 PROCEDURE:
5.1 User Department will return the dispensed materials to Warehouse in following conditions:
5.1.1 Cancellation of production plan.
5.1.2 After completion of batch processing.
5.1.3 After On-Line Rejection
5.2 Dispensed / Issued Raw Materials cannot return to Warehouse on any circumstances.
5.3 In case of cancellation of production plan, only packaging materials can be returned to Warehouse in their original issued packs on “Material Return Note” dully approved by QA as per Annexure-I in duplicate by affixing “Material Return Tag” along with “Material Dispensing Tag” which is defaced by making cross mark on it.
5.4 After completion of batch packing activity, packing department will reconcile the leftover material and return it to Warehouse on “Material Return Note”.
5.5 On receipt of excess material from user department, Warehouse personnel shall check the “Material Return Note” for QA approval then check for following details on “Material Return Tag” against “Material Return Note” and Material Issuance record i.e. BPR or Process Order, Materials Code, Material Description, A. R. No., Quantity Returned, Product Name, Product Batch Number etc.
5.6 If material not meets with the above details, inform to respective user department and QA. Send back the material to respective user department for rectification.
5.7 Warehouse shall not accept the printed labels or cartons with batch details and expired materials.
5.8 Keep the returned material in original “LOOSE” container / pack (wherever possible) at their original location along with the balance consignment.
5.9 If any material returned by user department which do not have balance stock in Warehouse, same shall be located on new location.
5.10 Ensure that the excess material returned from user department shall be issued first during next issuance.
5.11 On-Line Rejected materials shall be return by user department to Warehouse on “Material Return Note” along with dully filled and approved by QA “On-Line Rejection Note”.
5.12 On receipt of On-Line rejected materials from user department, Warehouse person shall check for availability approved stock of that particular A. R. No. and ask QA for balance stock (if available).
5.13 QA Head or designee shall decide about the balance stock of that particular A. R. No.
5.14 Warehouse person shall transfer the On-Line rejected material to rejected area along with balance stock (if instructed by QA).
5.15 Warehouse person shall inform to Purchase department about on-Line Rejection.
5.16 As per the comments received from Purchase department, On-Line Rejected Material can be send to vendor or destroyed it in factory premises.
5.17 On-Line Rejected Printed Packaging Materials cannot be returned to vendor, it should be destroyed in factory premises only.
6.0 ABBREVIATIONS:
MRN : Material Return Note
BPR : Batch packing record
A.R.No. : Analytical reference number
7.0 REFERENCES:
Nil.
8.0 LIST OF ANNEXURES:
Annexure-I: Material return note.
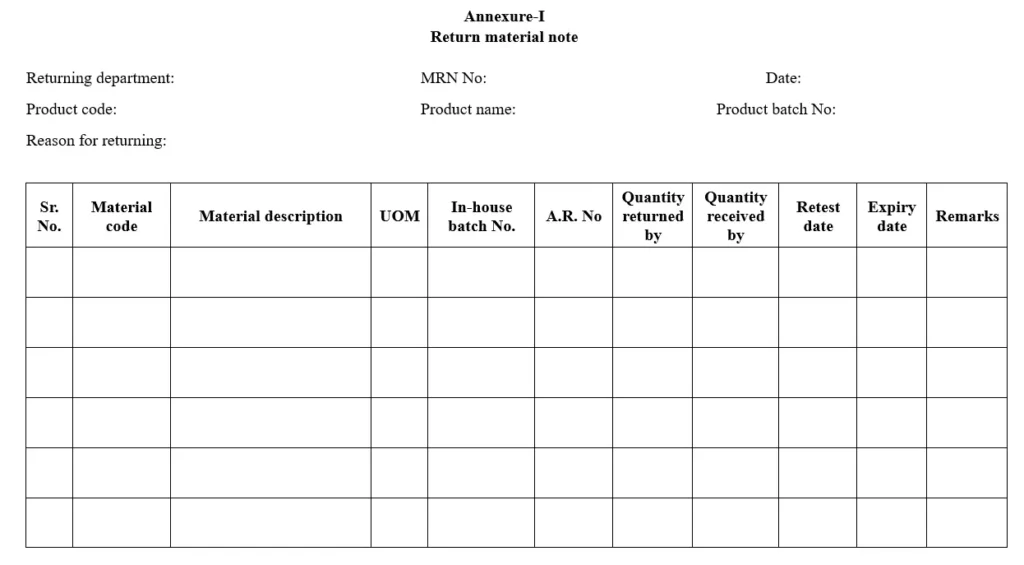